درجه تیرگی شیشه جوشکاری
-
ارسال شده توسط
مهدی محمدیان
- 0 دیدگاهها
درجه تیرگی شیشه جوشکاری
مبحث بسیار کاربردی و با اهمیتی که اکثر فعالان صنعت ، از آن غافلند .
درجه تیرگی شیشه جوشکاری
چرا که اگر بخواهیم درجه تیرگی را بیش از حد تنظیم کنیم ، به دلیل وضوح کم حوضچه جوش ، قادر به تولید یک اتصال استاندارد نخواهیم بود و اگر از طرفی درجه تیرگی پایین تر از حد استاندارد باشد ، به چشم های خود آسیب میزنیم .
مقادیر مناسب پیشنهادی توسط AWS در سند AWS F2.2 آمده که در ادامه فایل مربوطه پیوست شده است .
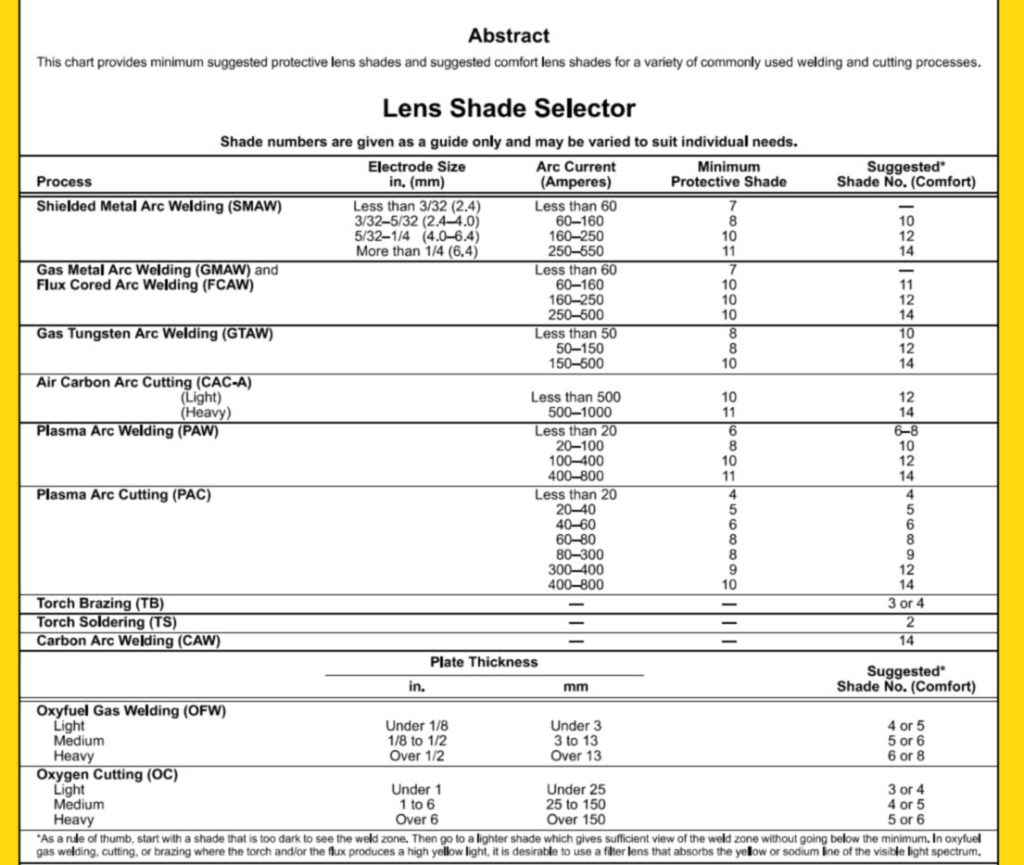
در جدول بالا ، چند ردیف و چند ستون مشاهده میشود . ردیف های متوالی ، فرایند های مختلف را نشان میدهد .
به بیان دیگر استاندارد خواسته تا برای هر فرایند ، عدد های مخصوص همان فرایند را ذکر کند .
به ترتیب این فرایند ها شامل :
- فرایند SMAW یا الکترود دستی
- فرایند GMAW یا FCAW که به ترتیب به جوشکاری CO2 و توپودری معروف میباشند .
- جوشکاری الکترود تنگستن که نام اصلی آن GTAW و یا TIG بوده و در ایران به جوش آرگون معروف است ،
- برشکاری با الکترود کربنی یا به عبارتی گوج کاری
- جوشکاری قوس پلاسما
- برشکاری پلاسما
از طرفی معنای دقیق 4 ستون جلوی هر ردیف به شرح زیر است :
- سایز الکترود : فقط در مورد جوشکاری الکترود دستی اعدادی را ذکر کرده که میتوان به آن اعتنا نکرد .
- arc current یا همان مقدار جریان
- حداقل درجه تیرگی پیشنهادی
- بهترین درجه تیرگی پیشنهادی
عملا در این فایل ، استاندارد بهترین درجه تیرگی را برای هر فرایند در هر مقدار آمپری ذکر کرده و همچنین تاکید کرده اگر بر اسای مقدار بهینه درجه تیرگی را تنظیم نمیکنید ، از عدد درجه تیرگی ذکر شده در ستون سوم کمتر تنظیم نکنید .
چند مثال
به عنوان مثال فرض کنید با فرایند جوشکاری آرگون با آمپر 130 جوشکاری میکنید .

به ردیف سوم از جدول ، ردیف مخصوص جوشکاری تیگ مراجعه میکنیم . از آنجایی که 130 عددی بین 50 تا 150 میباشد . به اعداد رو به روی 50 تا 150 دقت میکنیم .
بهترین مقدار تیرگی پیشنهادی ، مقدار 12 بوده اما چنانچه در این میزان تیرگی ، نمیتوانید به خوبی جوشکاری کنید ، استاندارد پیشنهاد داده از مقدار تیرگی درجه 8 پایین تر نیایید .

به عنوان مثال دوم چنانچه آمپر برشکاری پلاسما ، در 140 تنظیم شده باشد ، بهتر است درجه تیرگی شیشه محافظ جوشکاری ، 9 و حداقل 8 باشد .